The Sunspel Factory
Sunspel has been a family business for most of its 160-year history. Founded in Nottingham, the capital of Britain’s hosiery and lace industry, the business moved to its current Long Eaton location in 1937. Sunspel is the only brand to manufacture luxury T-shirts from its own factory in the UK. While the technology in our factory may have changed in the last 80 years, our commitment to community and a job well done remains the same.
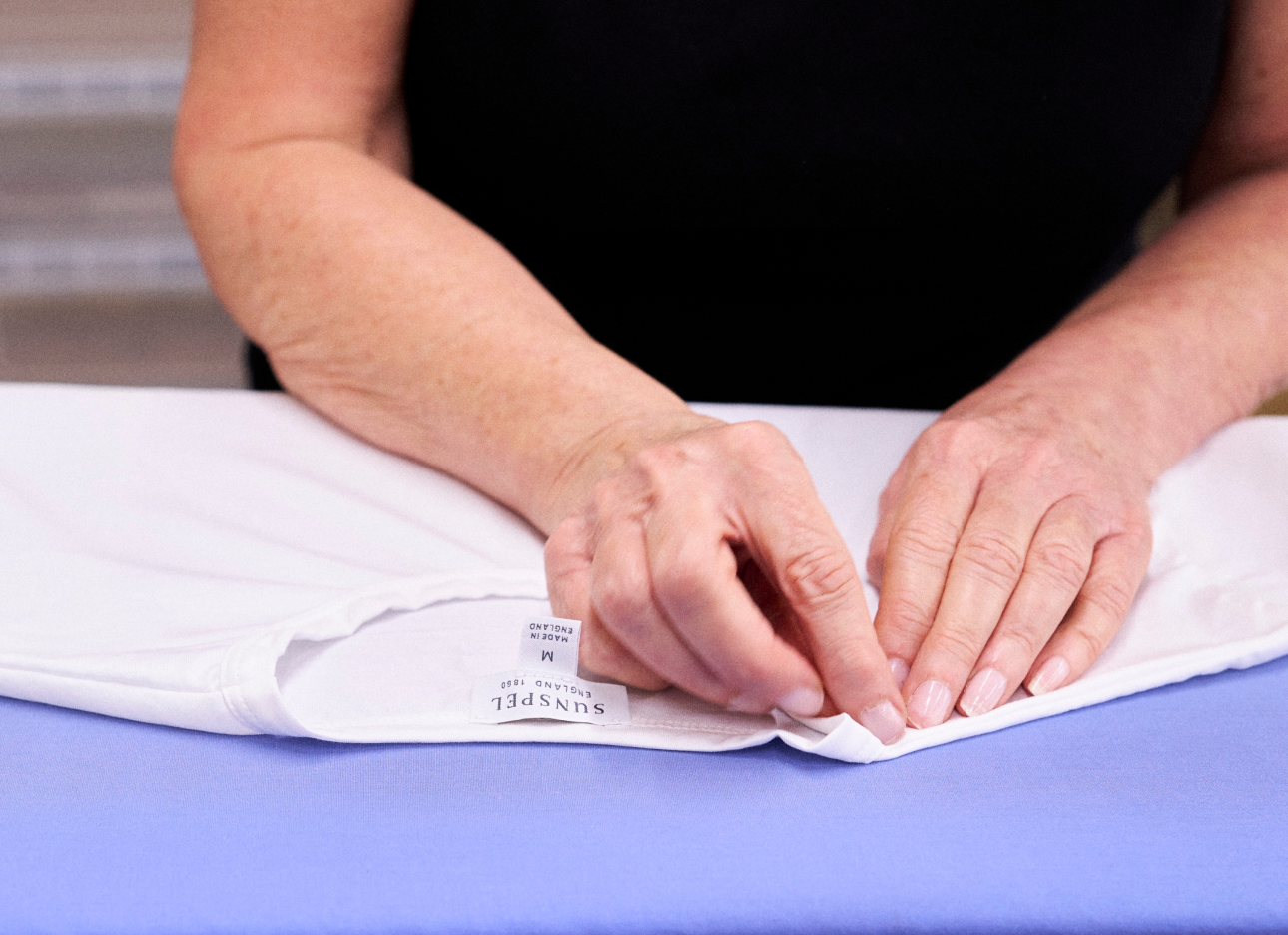
Today, we also work with other specialist factories in Britain and Europe. When we do, we apply the knowledge and expertise gained from our long experience to find the best. Many of the businesses we work with are small and family-owned, and they all share our beliefs about quality, ethical working practices and environmental responsibility.
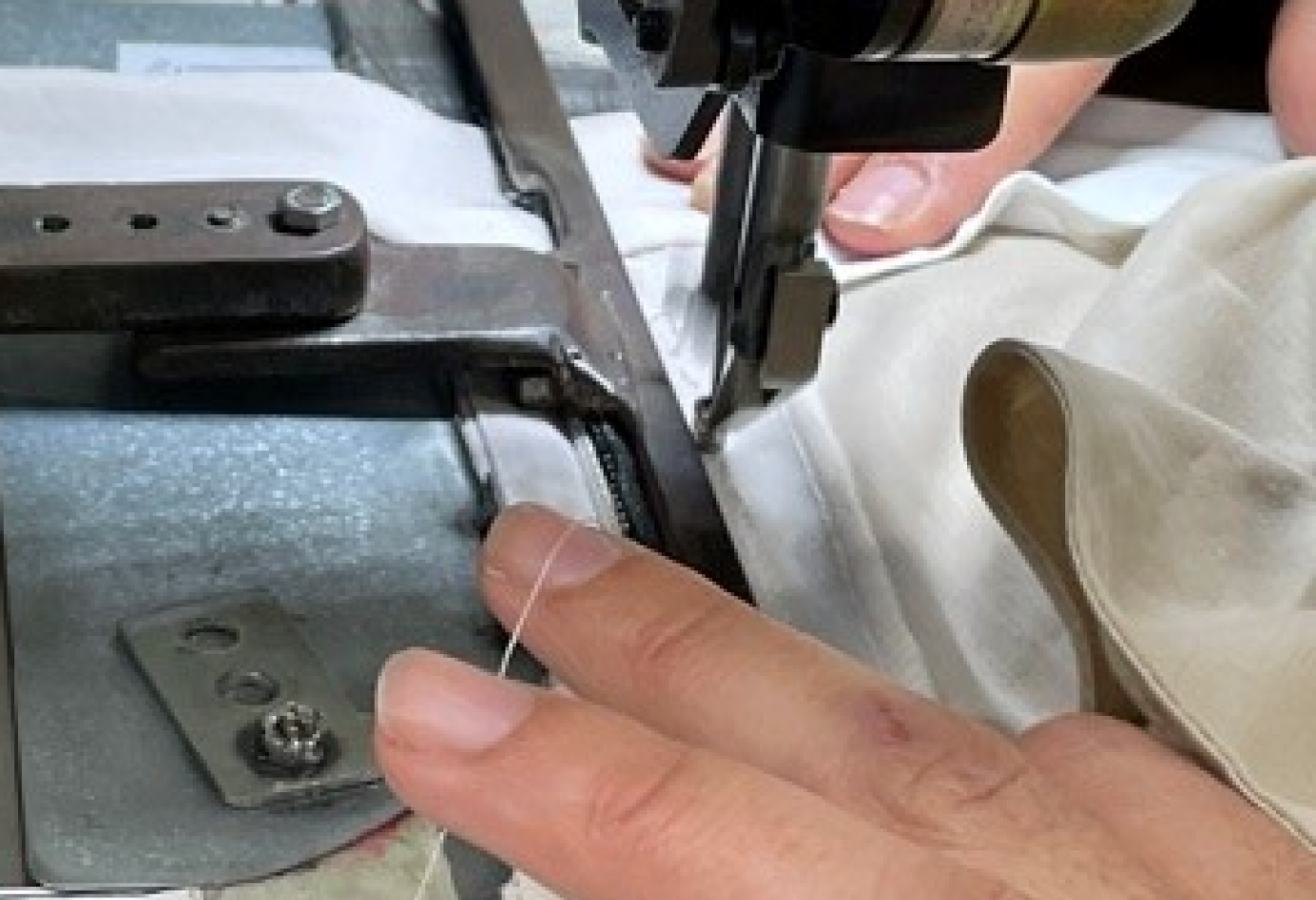
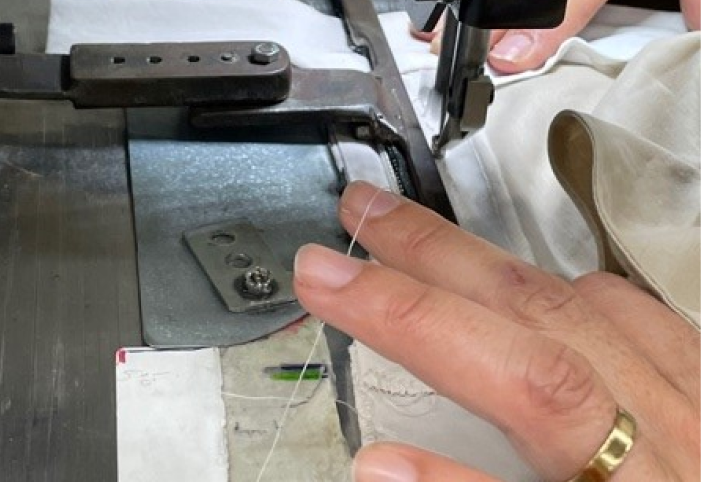
Sunspel’s polo shirts, sweat tops and cotton knits are designed in England and made by a family-owned specialist jersey factory in Barcelos, Portugal. Like all our partner factories they are committed to an ethos of craftsmanship and painstaking attention to detail.
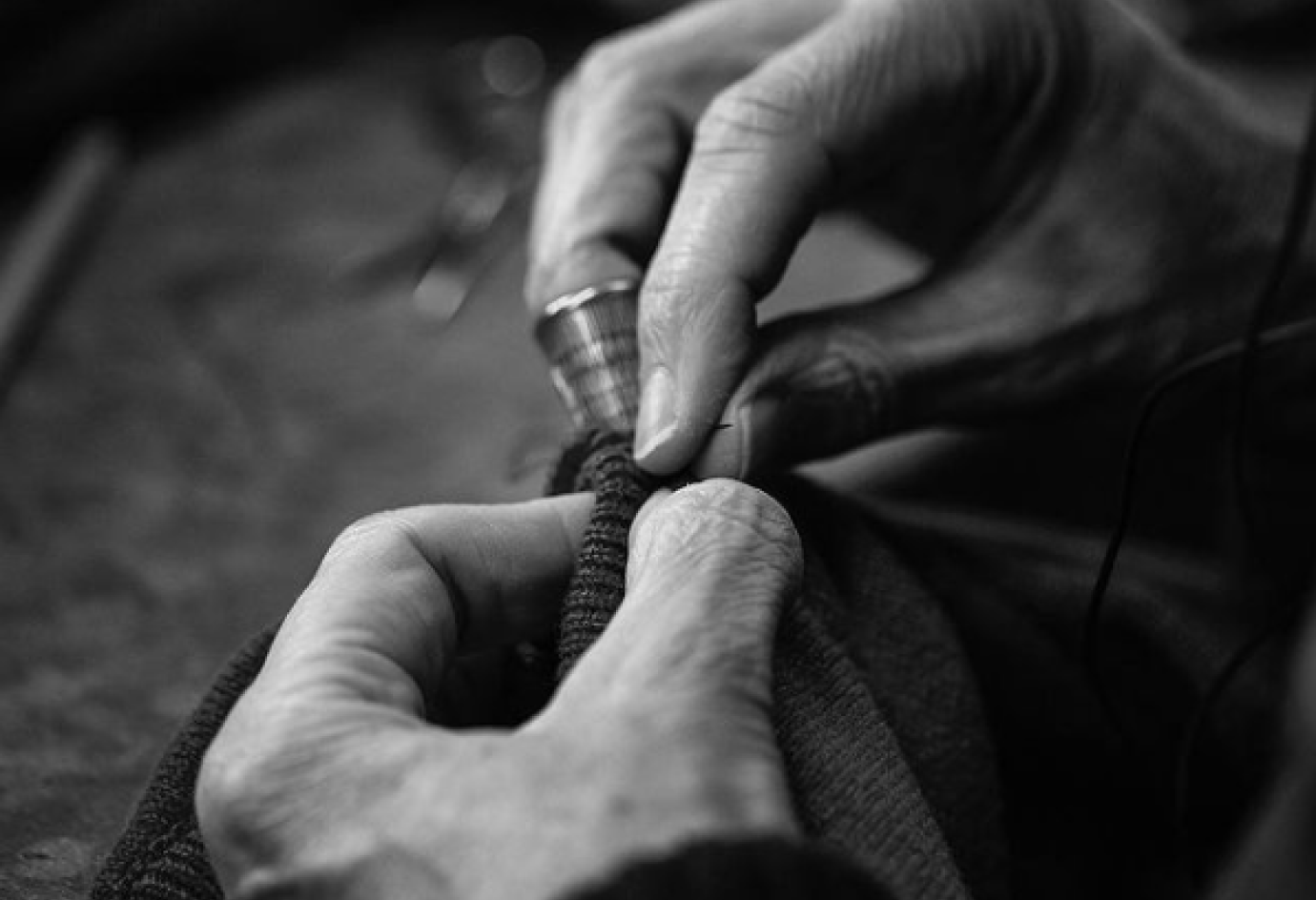
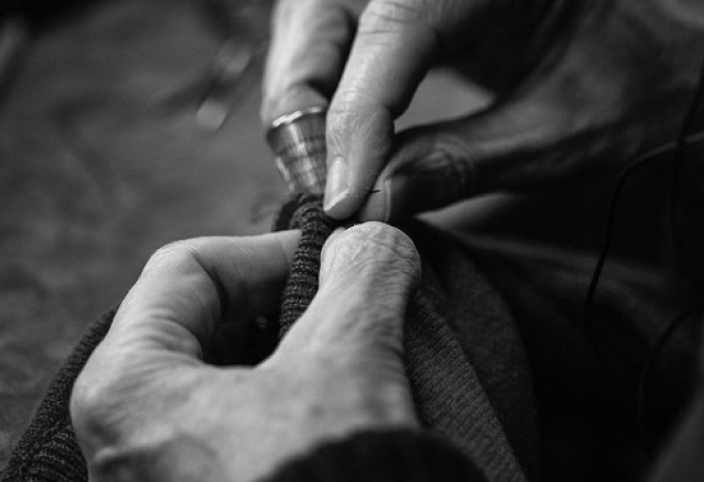
Scotland is internationally renowned for producing the finest knitwear in the world. Our cashmere manufacturers still use their original knitting machines from the early 1920s (no other machine is able to replicate the quality of the knit) and they hand-finish each Sunspel garment using techniques passed down from generation to generation, resulting in garments that feel luxuriously soft and will last for many years.
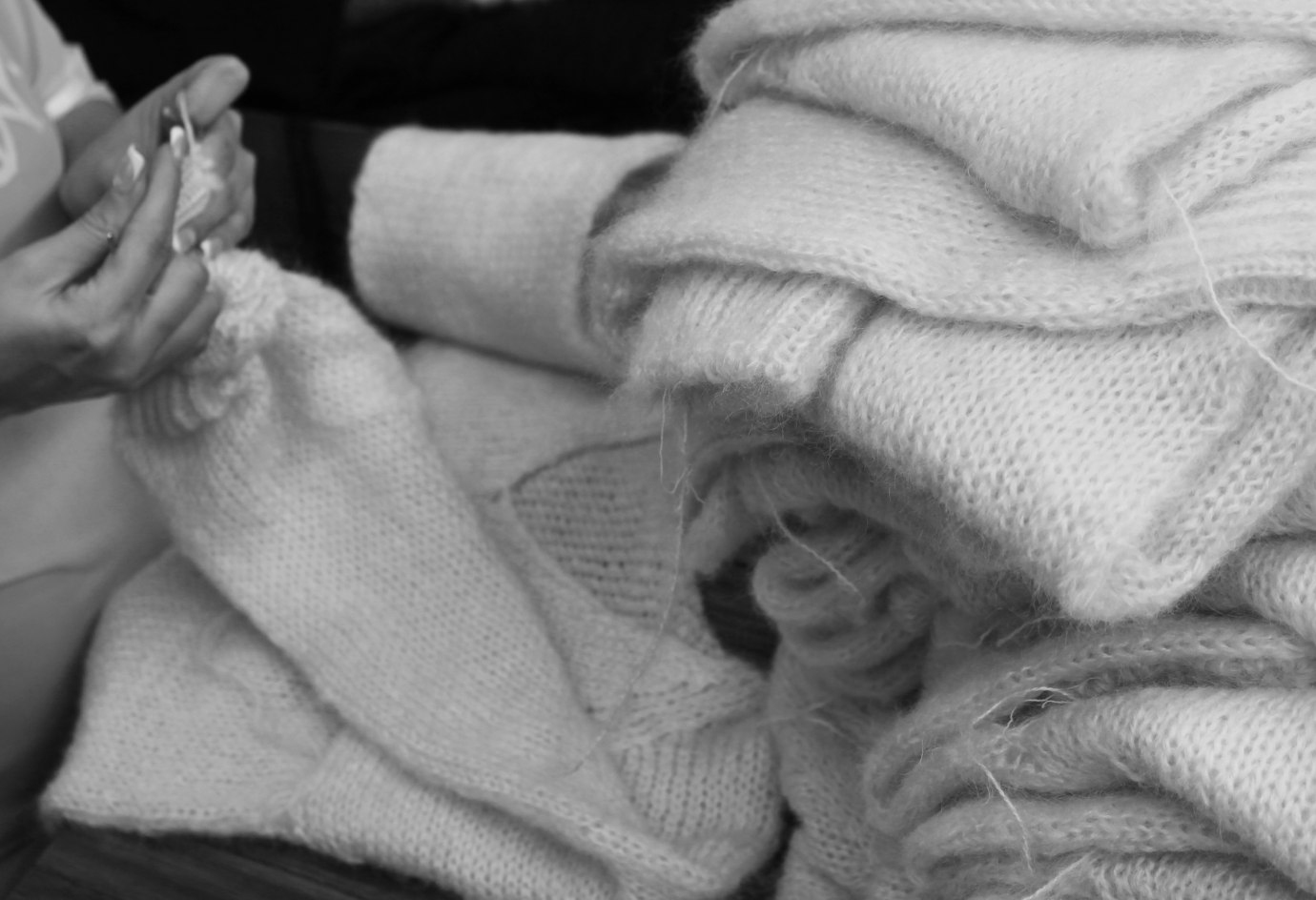
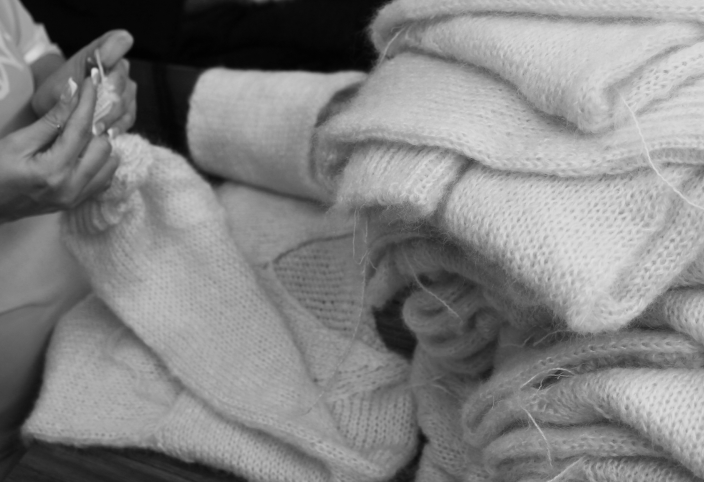
Our Scottish lambswool manufacturers have a rare specialism in working with this raw fibre and elevating it through expert finishing. Both of our Scottish partners work with premium yarns supplied by Scottish spinners Todd and Duncan, who use the pure water of Loch Leven to create exceptionally soft yarns.
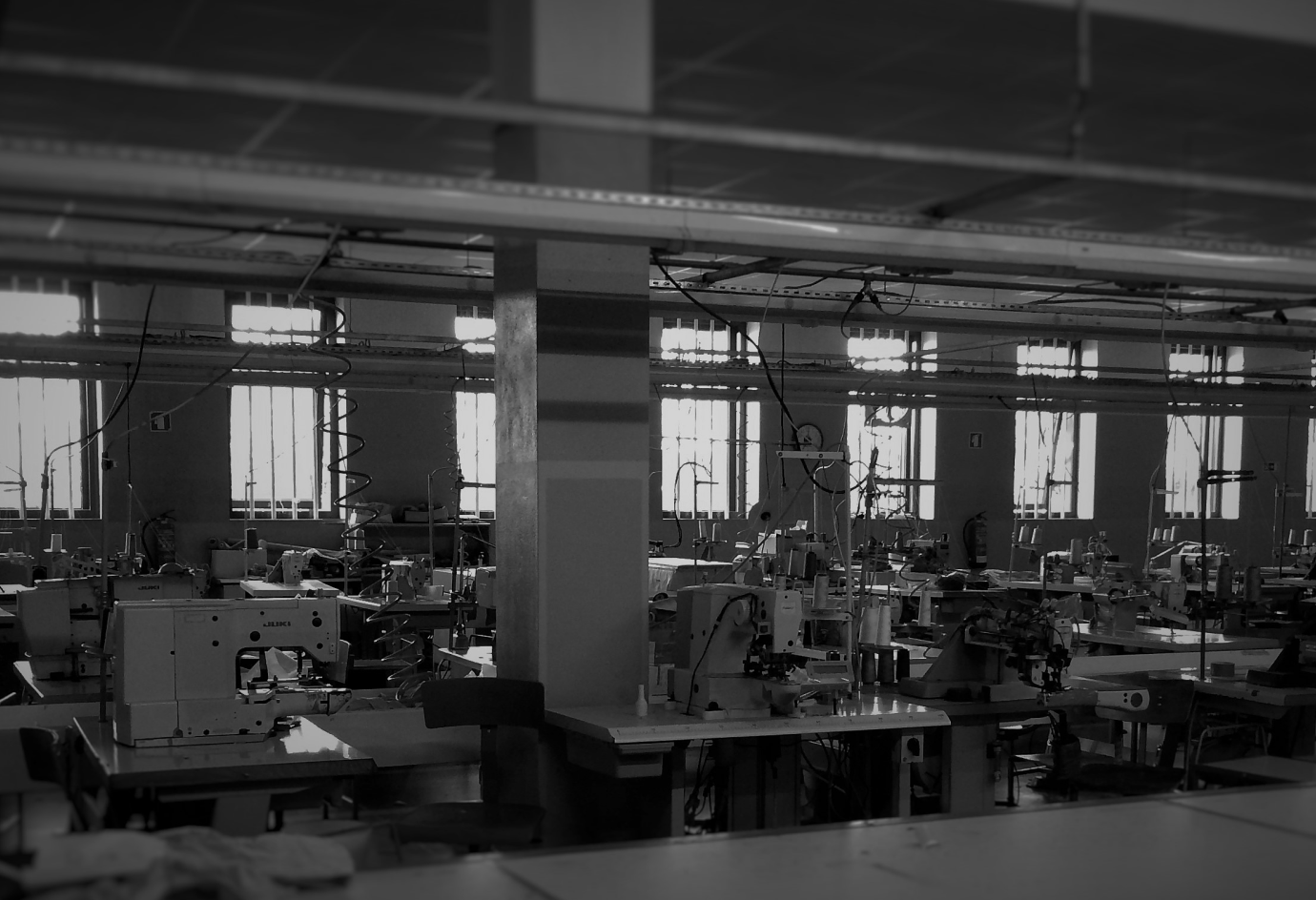
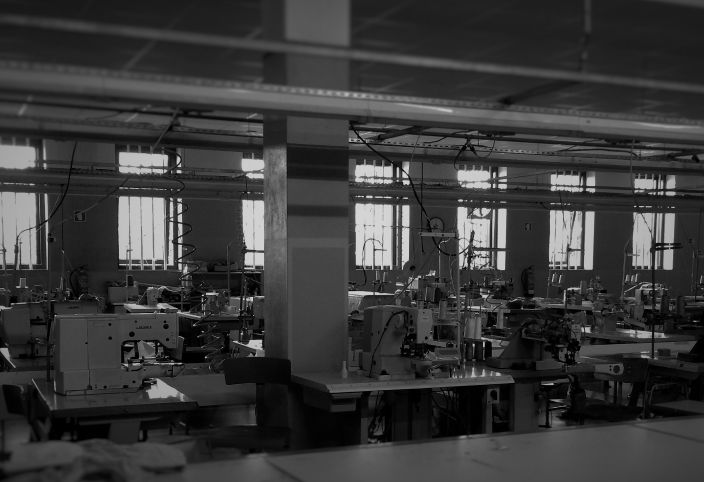
The British Boxer Short was invented by Sunspel’s owner John Hill in 1947.
Today we work with a specialist family-owned manufacturer in Portugal, to make the classic Boxer Short to a design the same as Hill’s original specification.

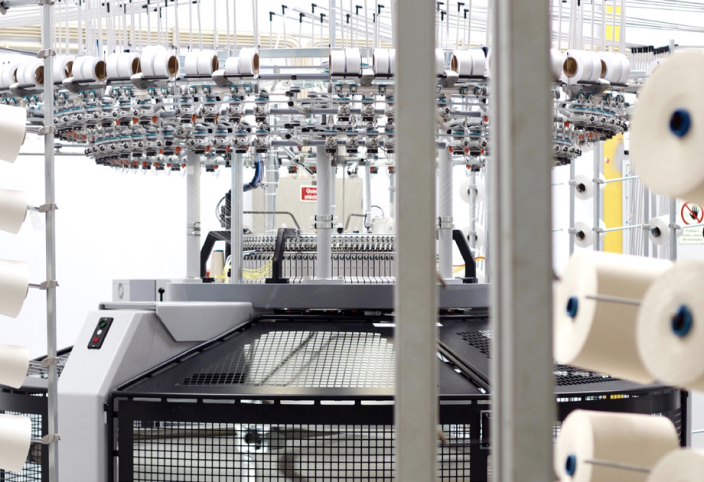
Sunspel has been making luxurious cotton underwear since the 19th century. The family-owned manufacturer we work with now has a similar structure to the very first Sunspel factory in Nottingham’s lace district. It is a fully vertical factory, meaning both the kitting and garment manufacture is under the same roof – making it a perfect partner for our entire jersey underwear range.
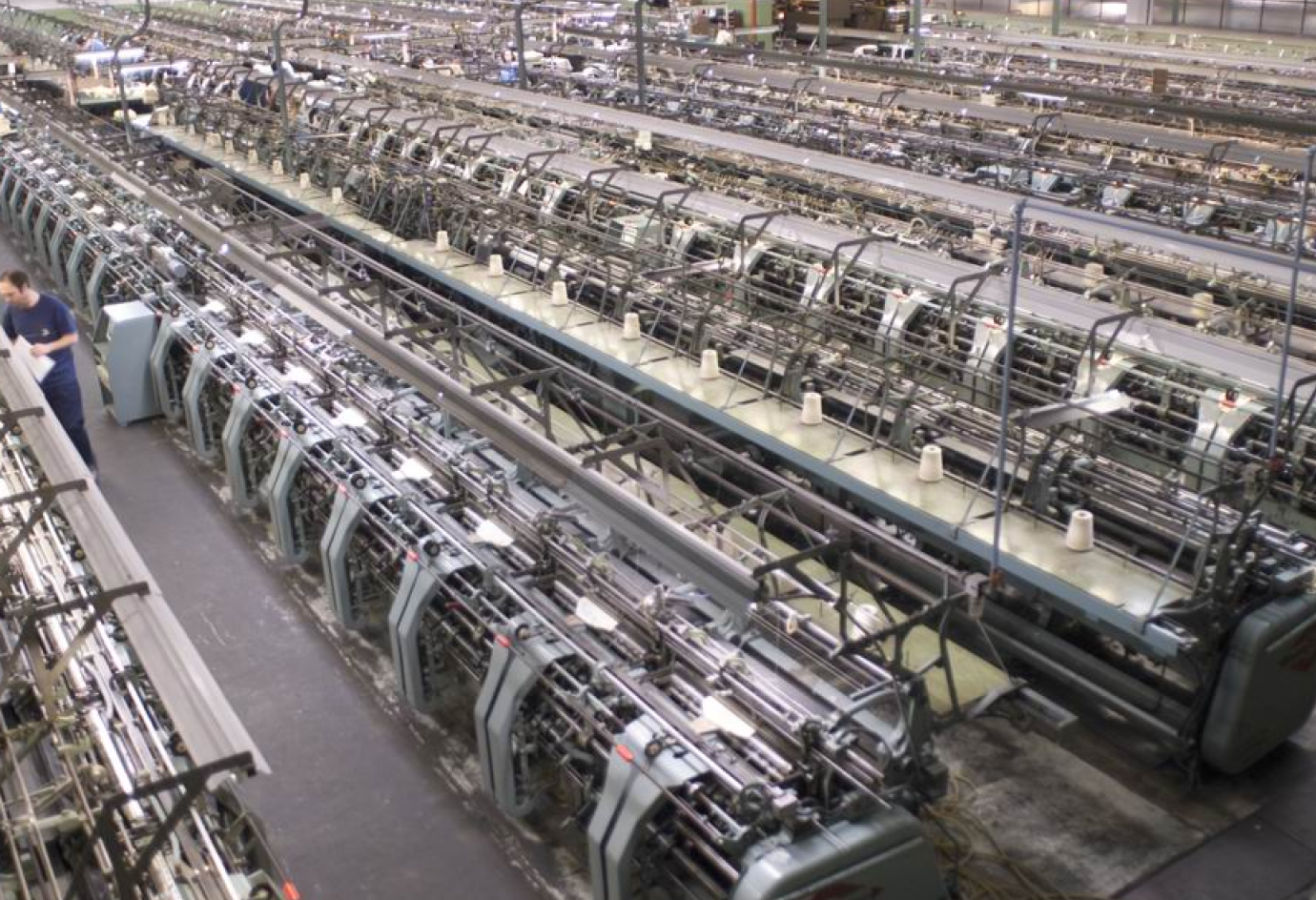
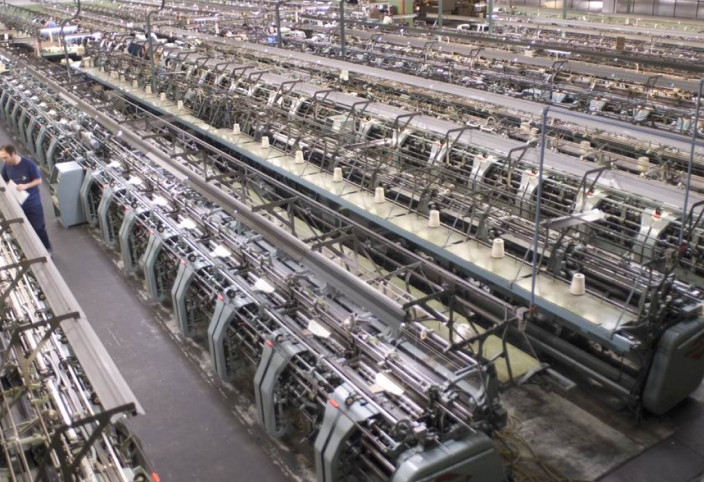
Sunspel’s merino jumpers and knitwear are made from an exceptionally soft extra fine wool yarn, which requires particular skills to knit. We work with a factory that specialises in traditional flat bed frame knitting, using vintage 1960s Bentley cotton machines fitted with bespoke needles that can give a refined, flat finish to extra fine gauge knitwear. There is a close and natural affinity between the craftsmen of Braga and the Sunspel ethos: the knitting techniques – and indeed the Bentley machines themselves – were originally from Loughborough, not far from our own factory in Long Eaton.
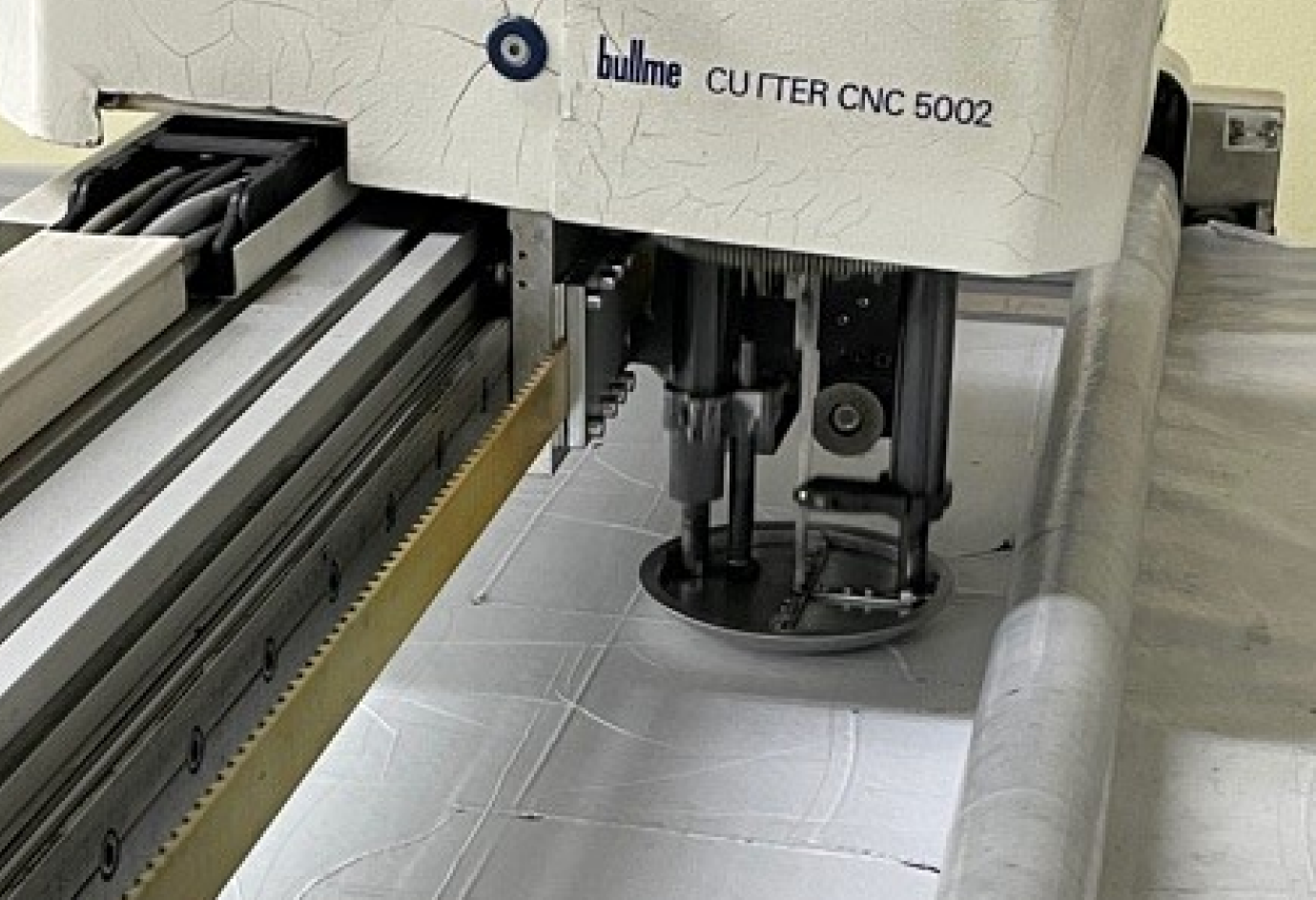
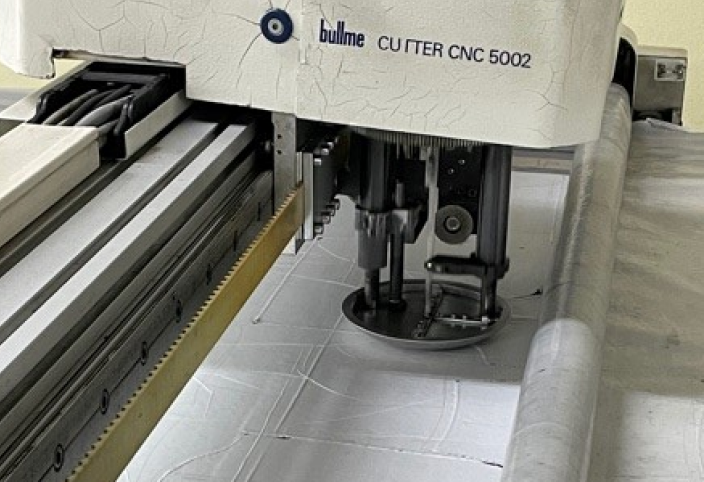
Sunspel’s woven jackets and trousers are designed in England to be of the highest quality, durability and comfort. We work with specialist manufacturers in Pedroso, Portugal to make our casual tailoring to our exact specifications.
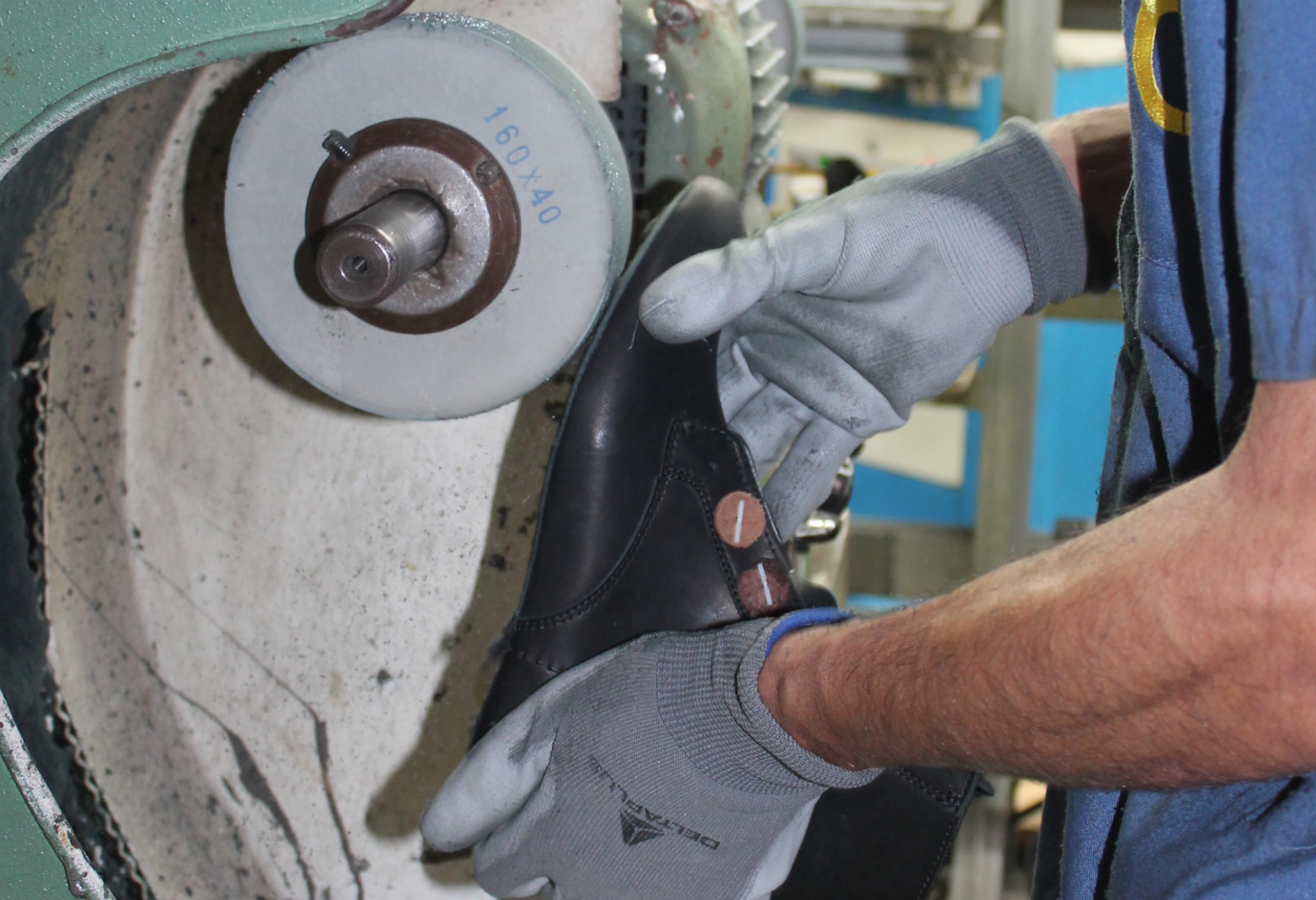
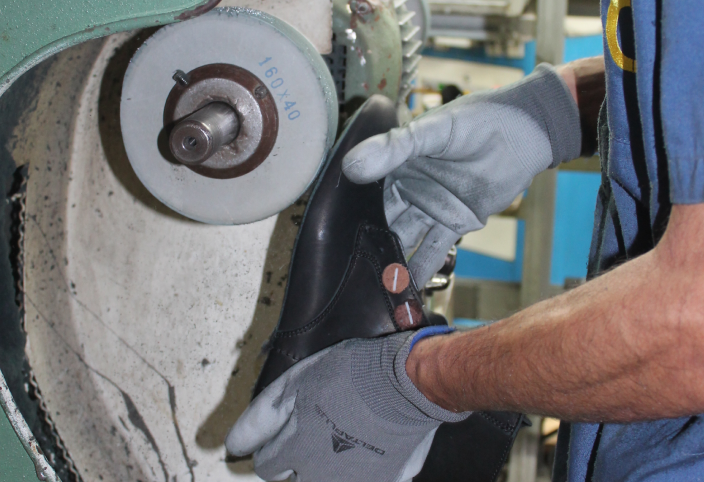
Sunspel’s tennis shoes are produced by an independent factory based on the hills of Santo Tirso. They have built a worldwide reputation for exceptional quality and innovation in shoe making. Everything is handmade, so expert care and craft goes into producing the best quality, most comfortable sneakers.
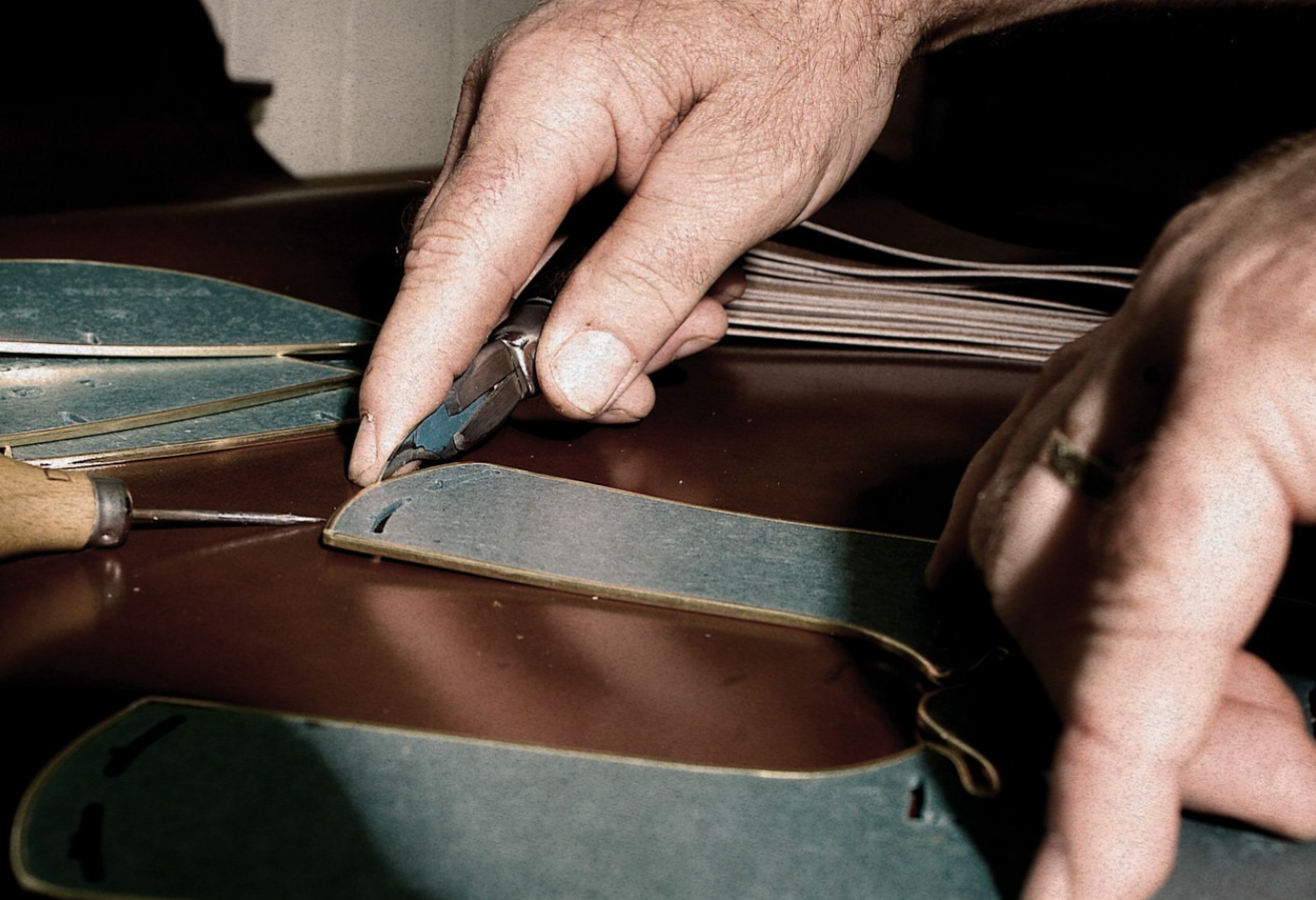
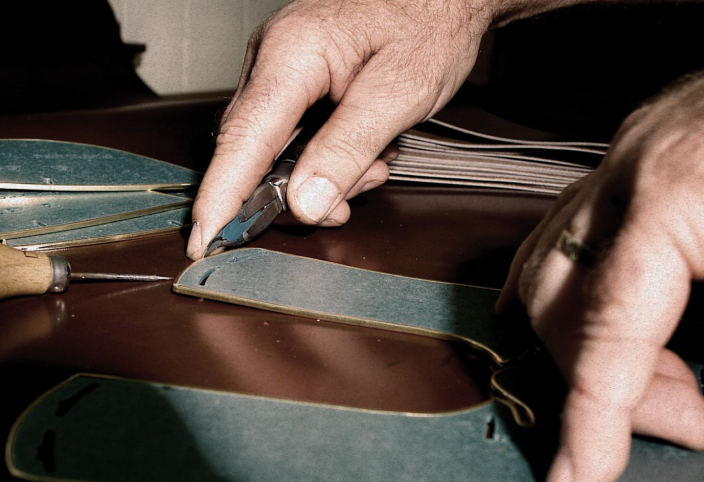
Our footwear is supplied by the longest-established shoemaker in England – still situated in Northampton and owned by the fifth generation of the same family. Every single pair of boots or shoes is the result of 260 individual processes, each of them are carried out by experienced master shoemakers – resulting in footwear that will last a lifetime.
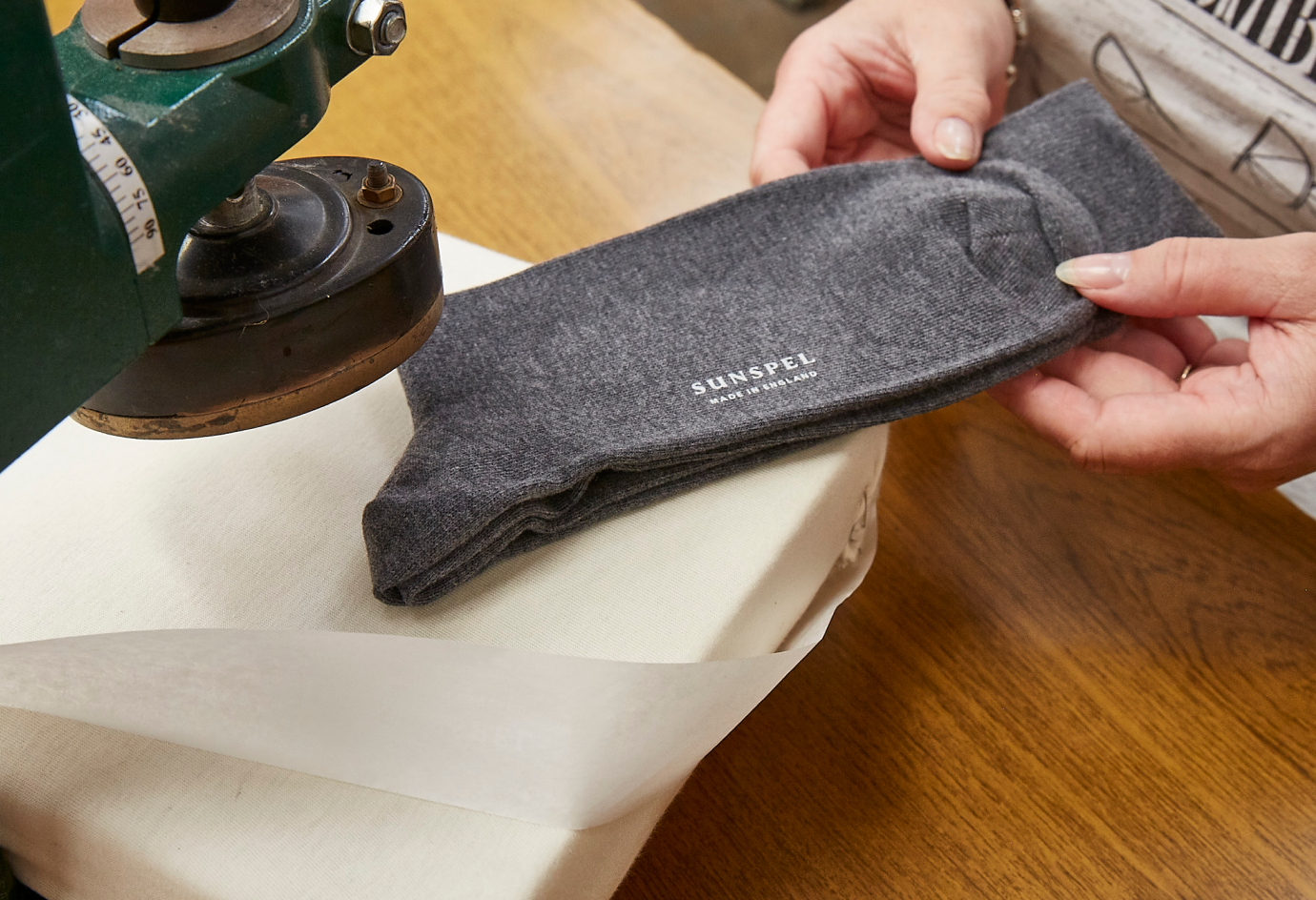
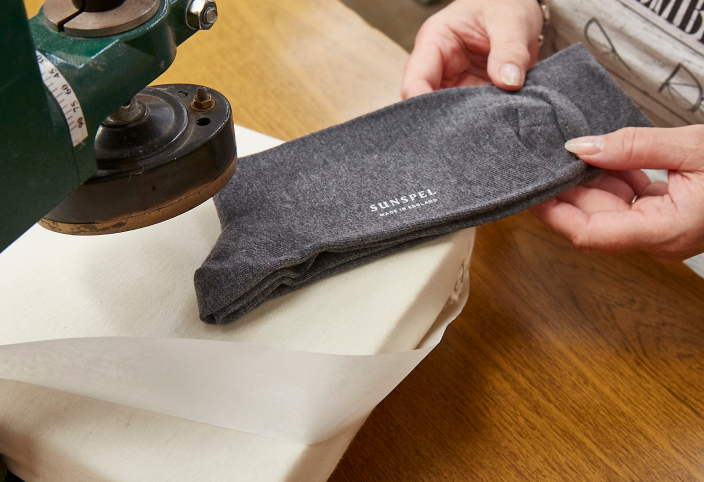
Sunspel’s range of socks is manufactured by one of the oldest hosiers in the UK – a family-run business renowned for using the finest natural fibres for luxurious quality, durability and supreme comfort.
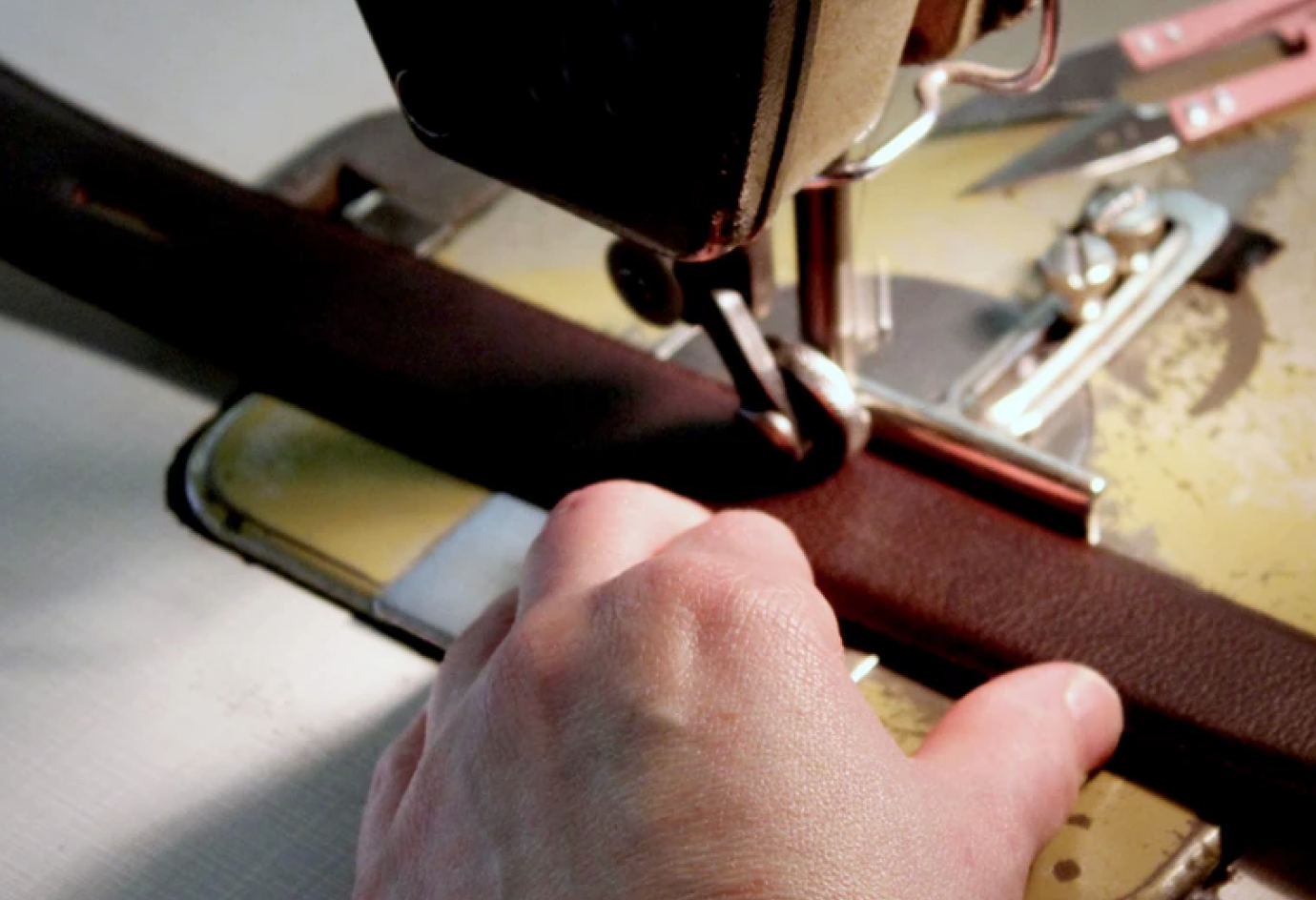
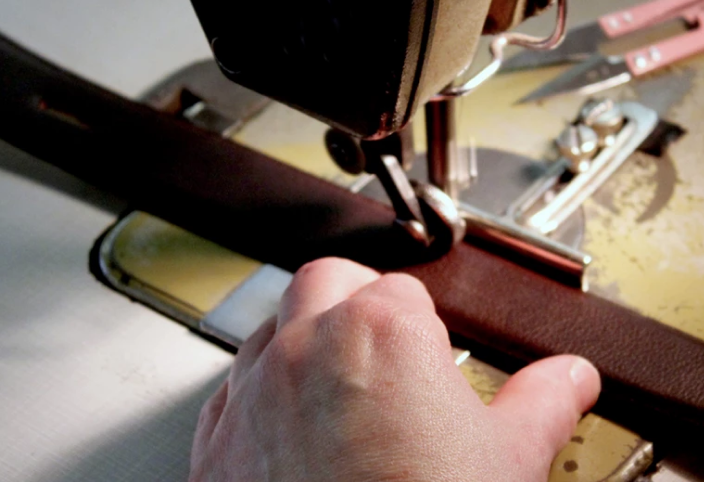
Sunspel’s belts and leather accessories are made to last by a specialist business founded in 1946 that is still family owned. The company sources the finest quality leathers and employs traditional crafting skills passed down the generations.
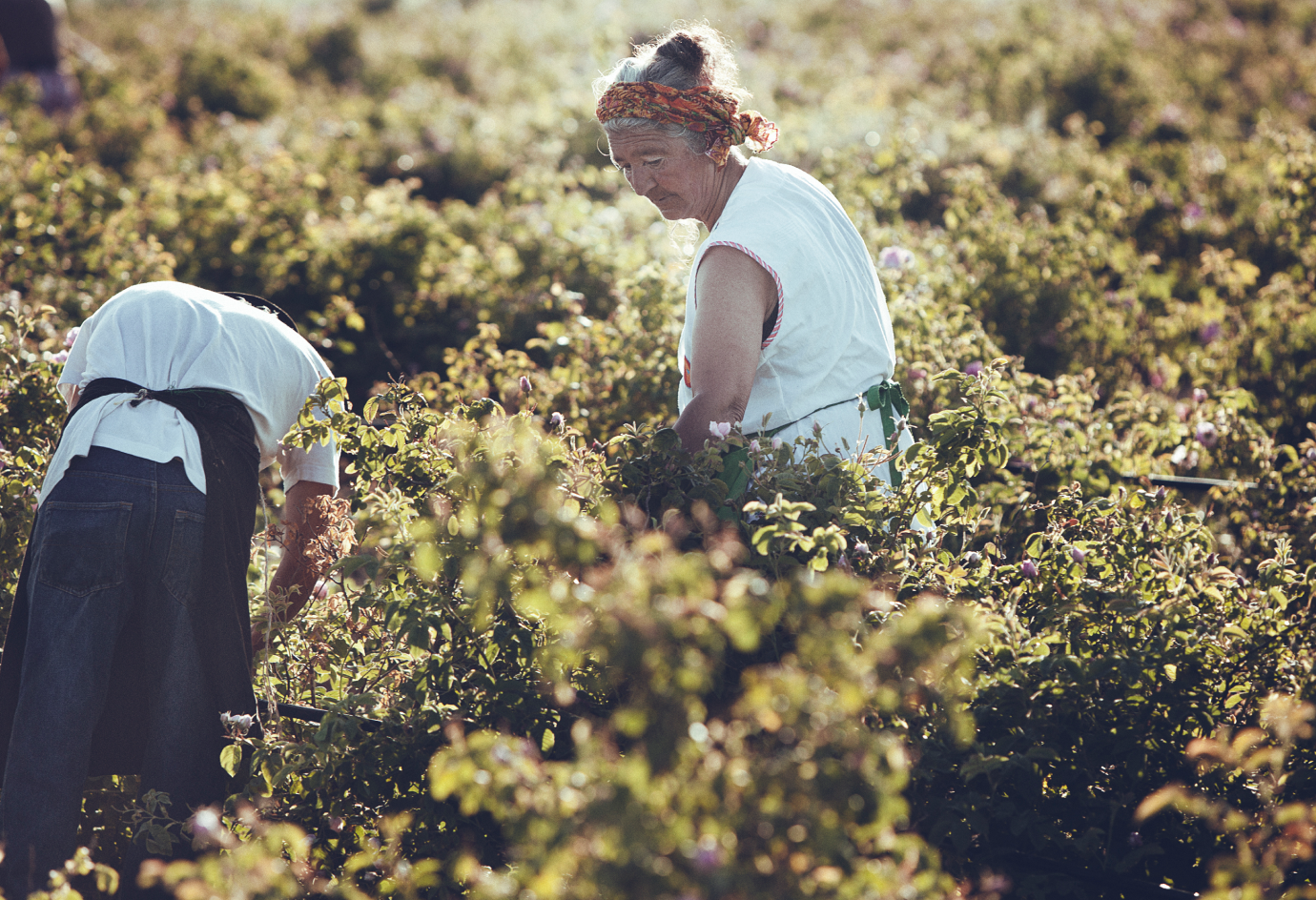
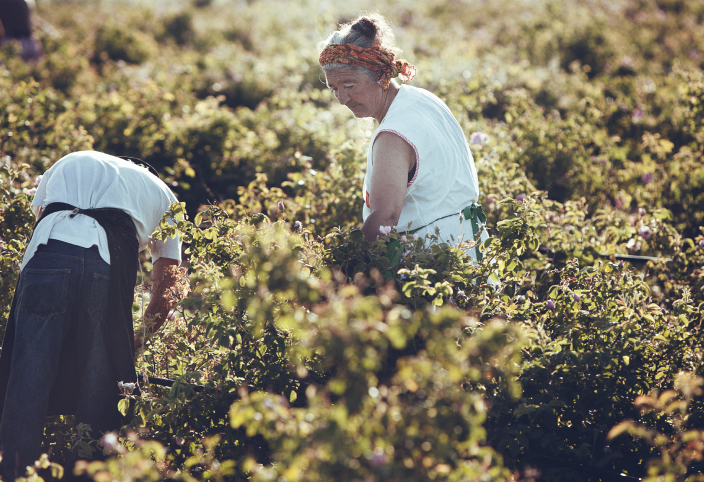
Sunspel’s fragrances are made in Grasse, which has had a perfume industry since the late 1700s. We work with a French family business in Grasse that has been at the forefront of its industry for 170 years, and is the world leader in sustainable, natural ingredients for fragrances and candles.
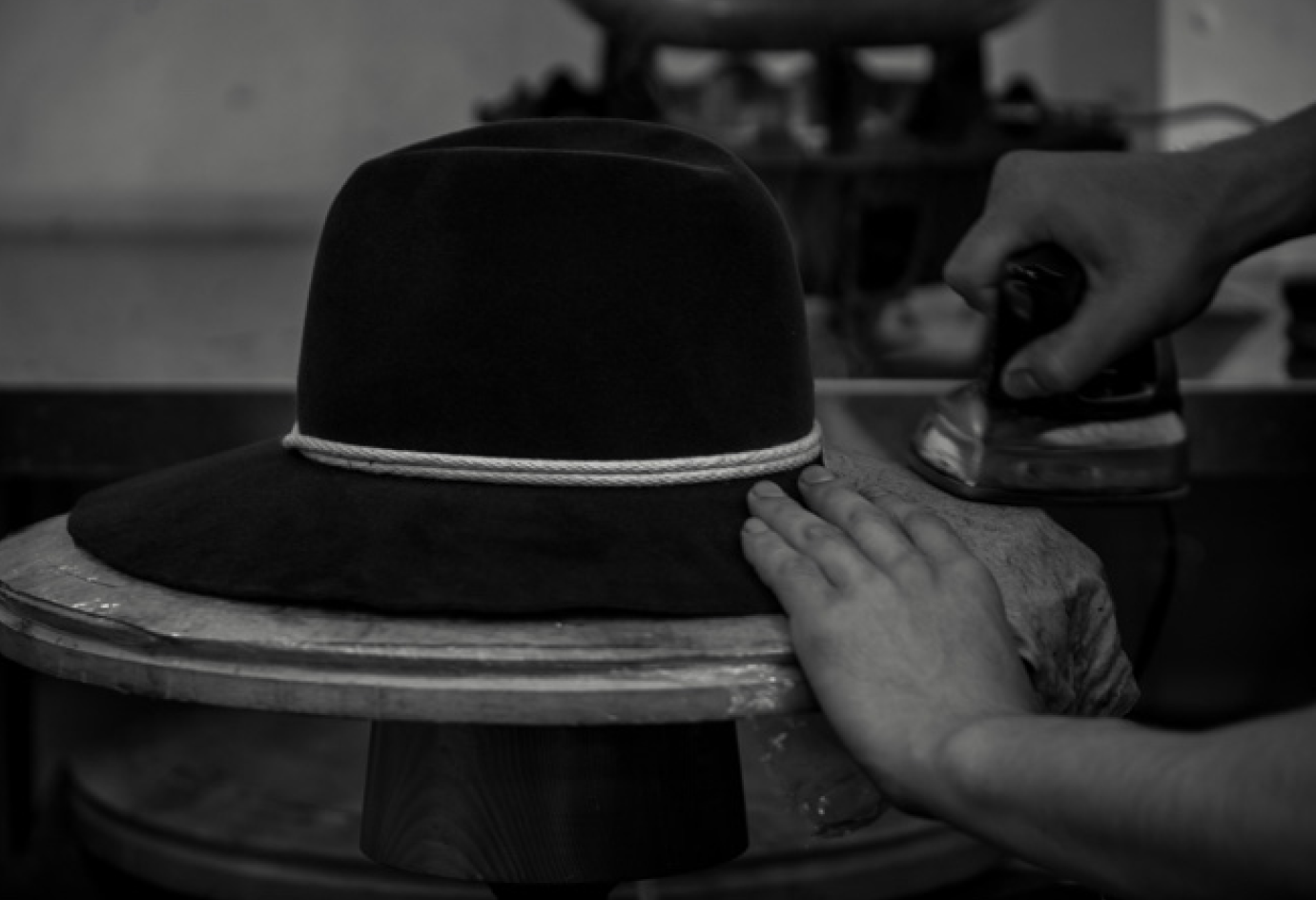
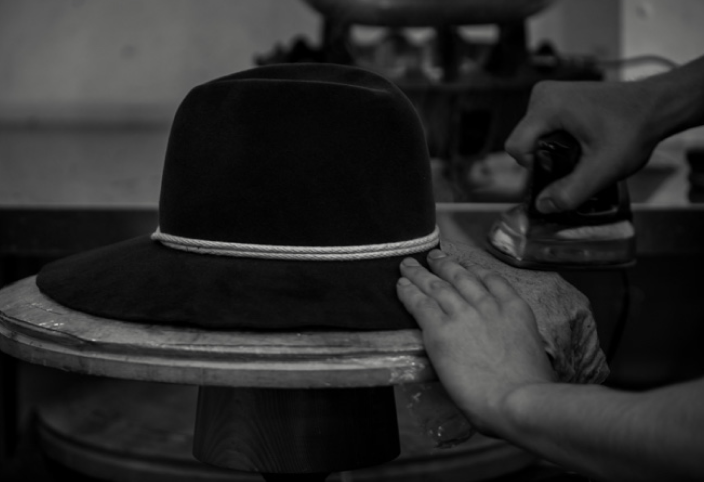
Our Japanese paper hats are handmade by a specialist milliner who uses traditional artisanal techniques that cannot be replicated with mass production.
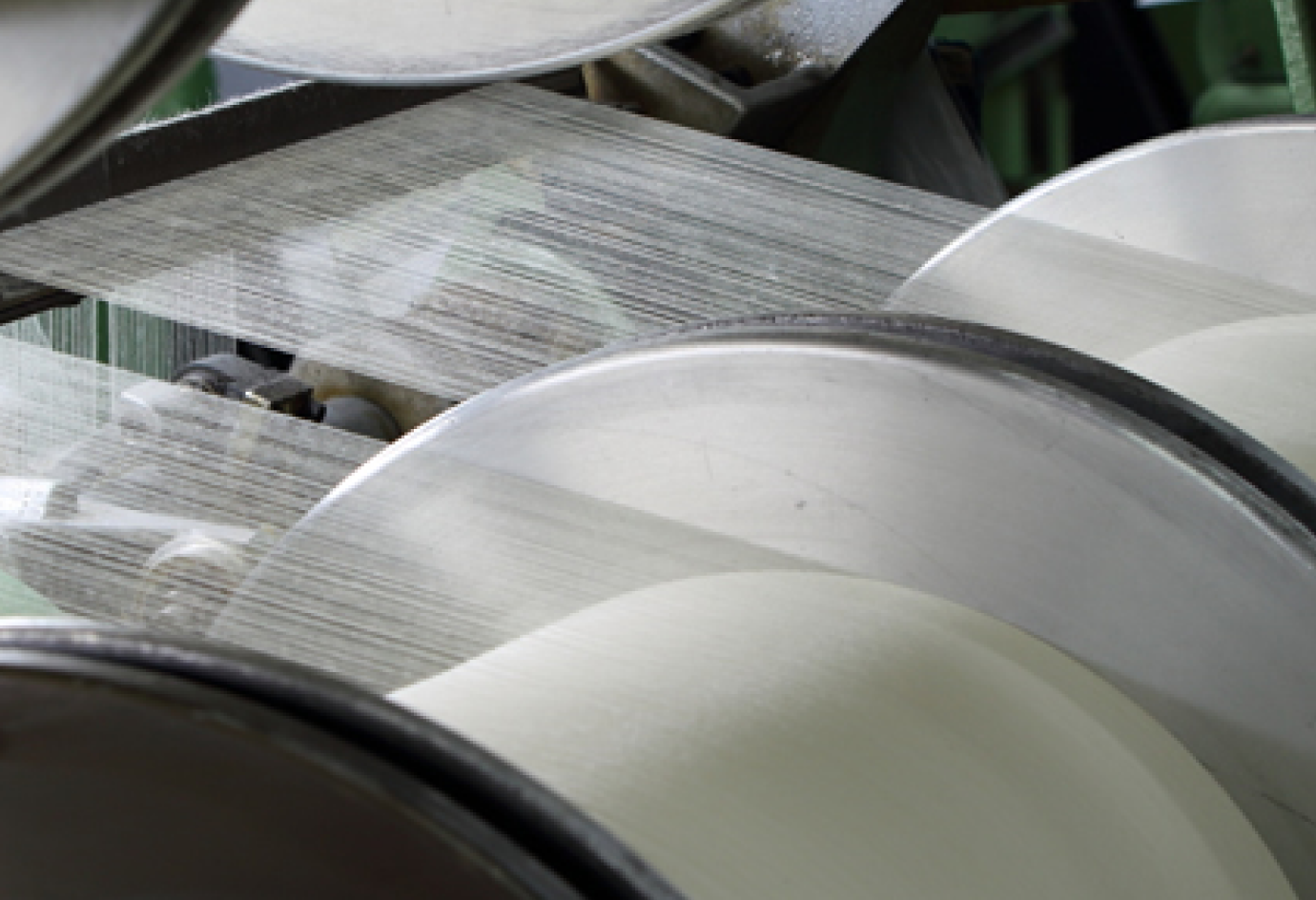

Warp knitted cotton is a key part of Sunspel’s heritage of innovation, dating back to the early 20th century when we adapted lace warp knit machines to create a unique smooth, lightweight cellular cotton fabric for our underwear, T-Shirts and Polo Shirts. These ground-breaking fabrics remain popular to this day, and traditional warp knitting remains the only way to make them. Today, we work with a factory in Portugal that uses extremely rare 70-year-old warp knit machines. We have calibrated these machines to knit our classic cellular fabrics (Q14 and Q75) in line with their original and unique specifications.
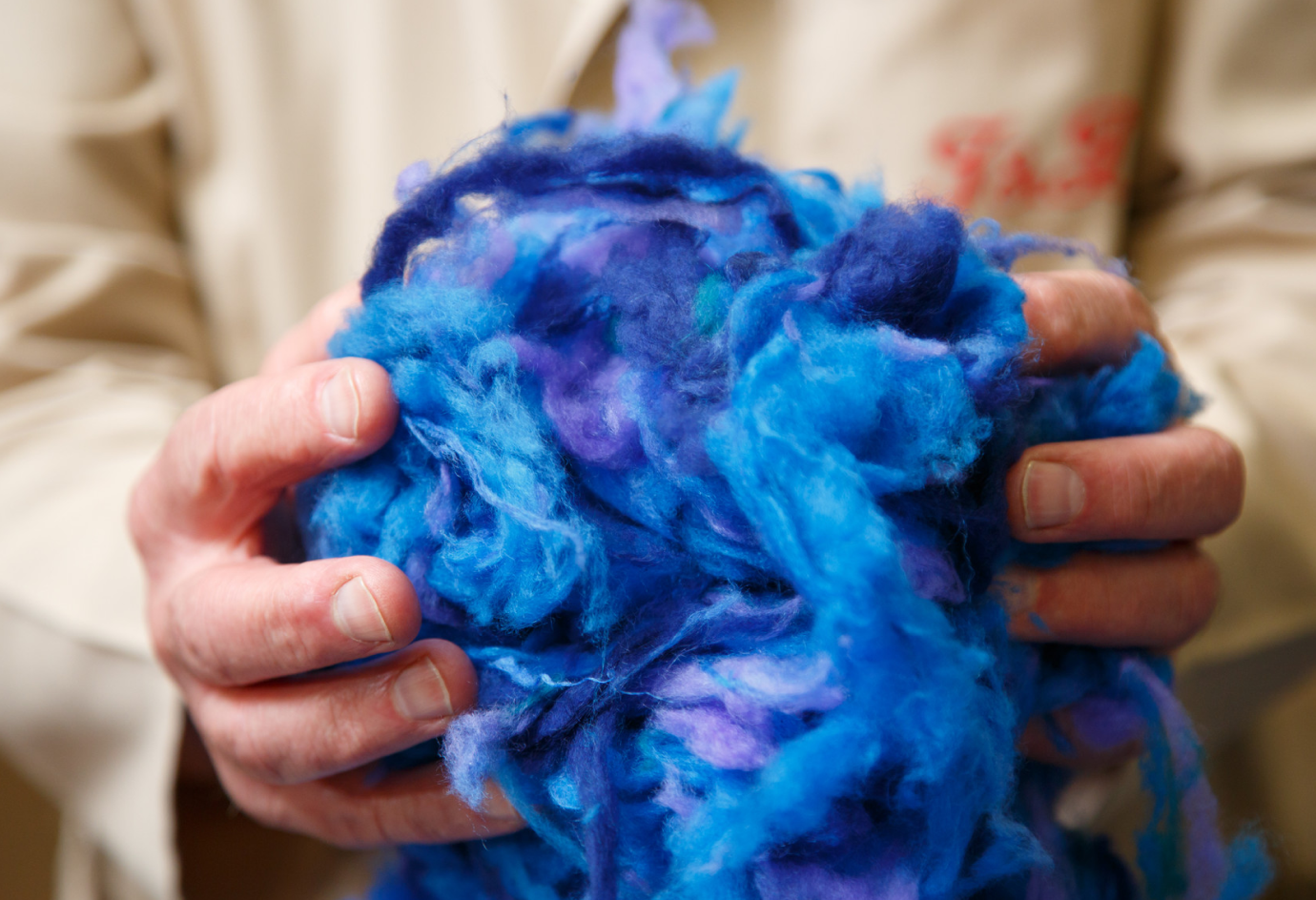
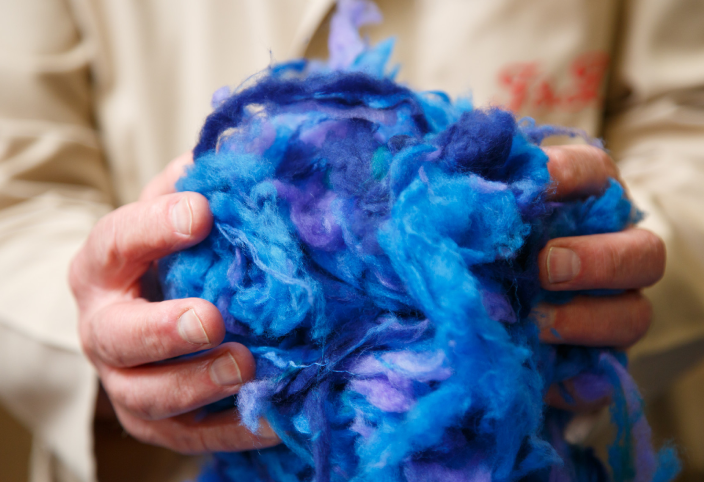
Since 1897, Todd and Duncan have been spinning yarn on the banks of Loch Leven in Kinross, where they have a limitless supply of the softest, purest Scottish water. It is this water that gives their yarn its exceptionally soft hand feel. All the water used is cleaned and returned to the Loch, so no resources are wasted. Every batch of raw fibre is personally checked for quality, and all yarns are carded and spun on mules: a traditional process that is slow and painstaking, but no other technique can recreate the exceptional feel and handle of the Scottish wool.
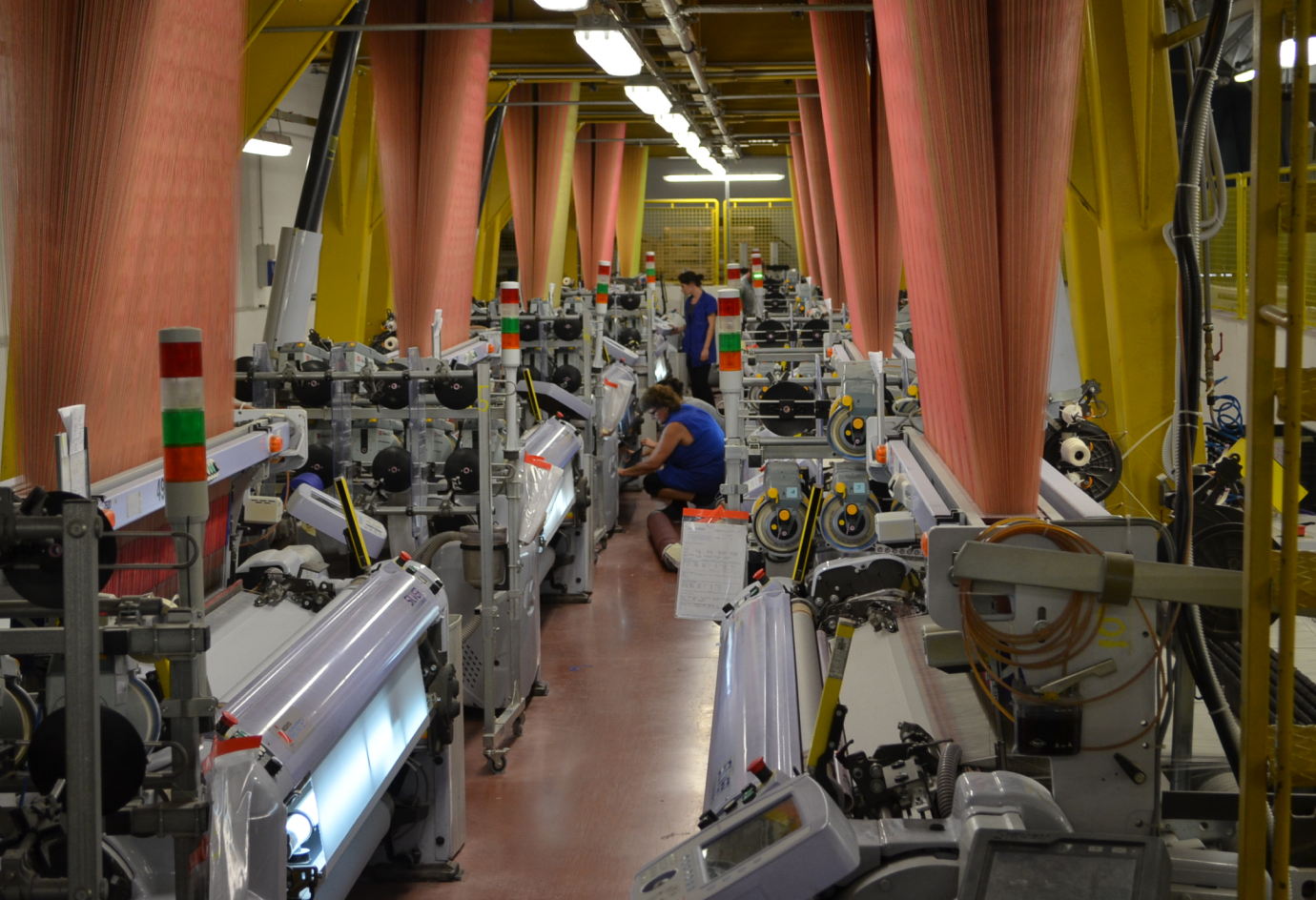
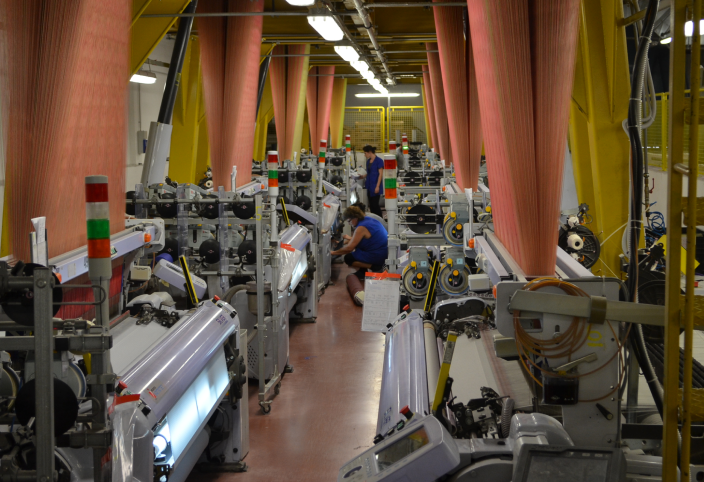
For Sunspel’s luxurious Italian shirting ranges we sought out the very best fabric specialists in the country. Our brushed cotton flannel, denim and chambray shirts are made by weavers in Como who are committed to sustainability and waste-free manufacturing, with eco-friendly approaches to all aspects of their business from
energy supply to packaging.
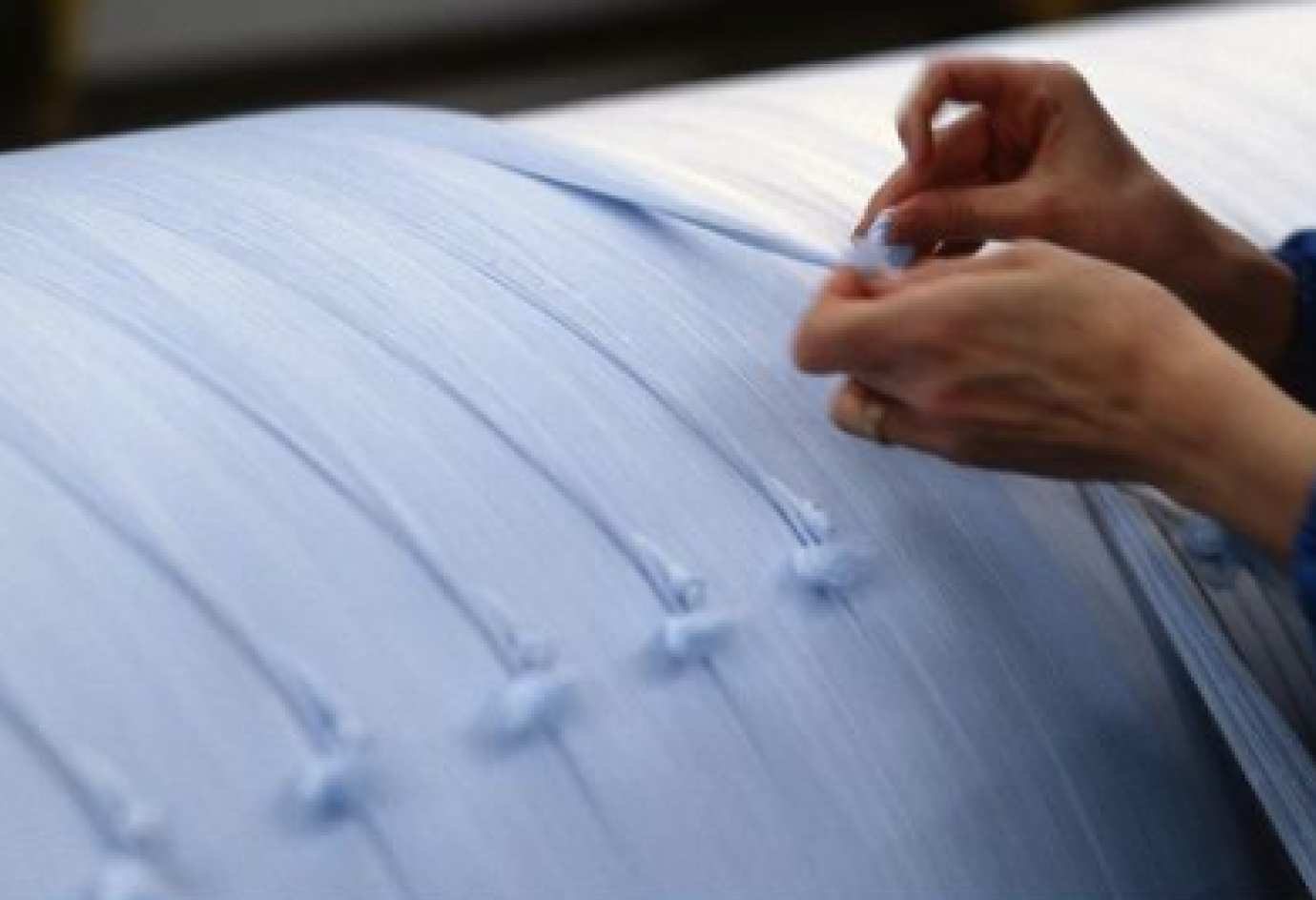
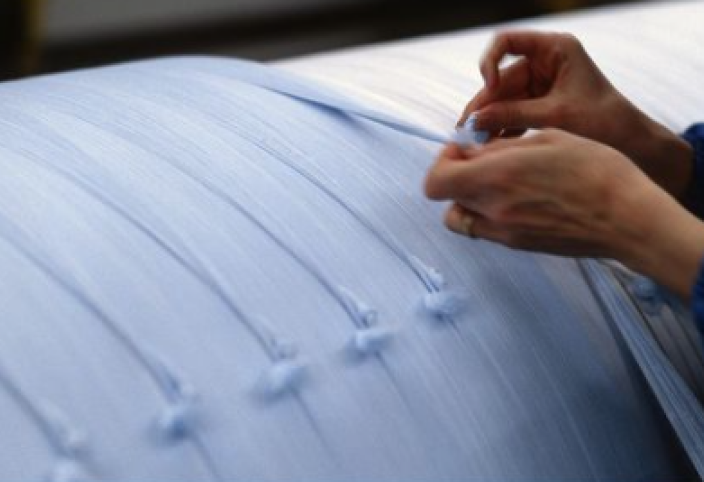
Our premium Italian linen shirting is woven by a business established in Treviso by three brothers in 1911. Still family-run, they specialise in weaving exceptionally fine yarns and are renowned throughout their industry as the benchmark for quality.
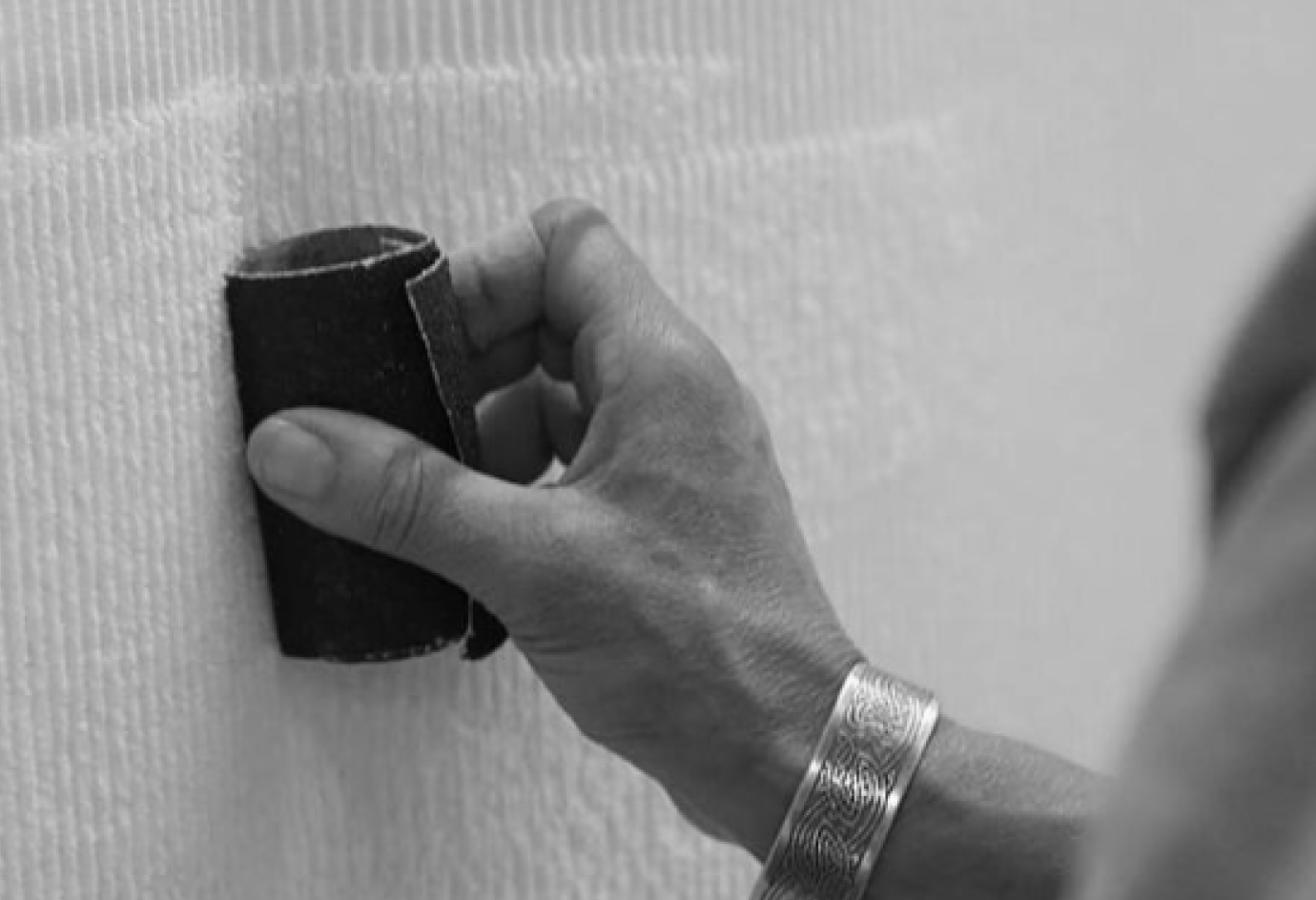
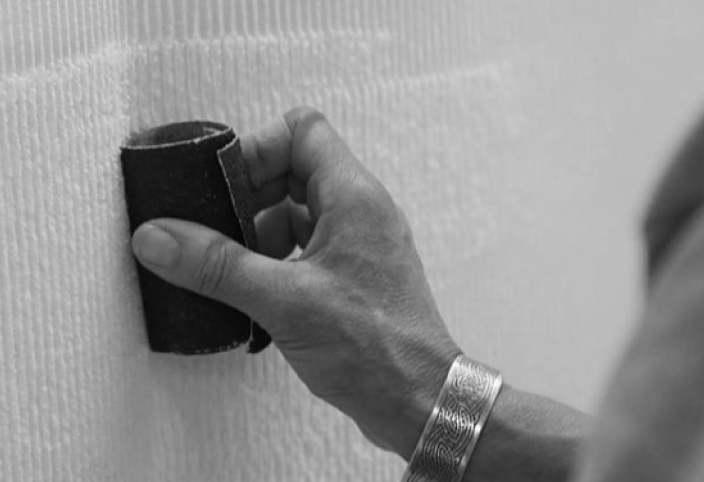
Sunspel’s luxury corduroy and cotton-linen fabrics are crafted by one of France’s finest heritage manufacturers with a history dating back to 1828. Like Sunspel, they continue to innovate new methods and sustainable textiles. All fabrics conform to OEKO-TEX standards, ensuring zero ecological harm.
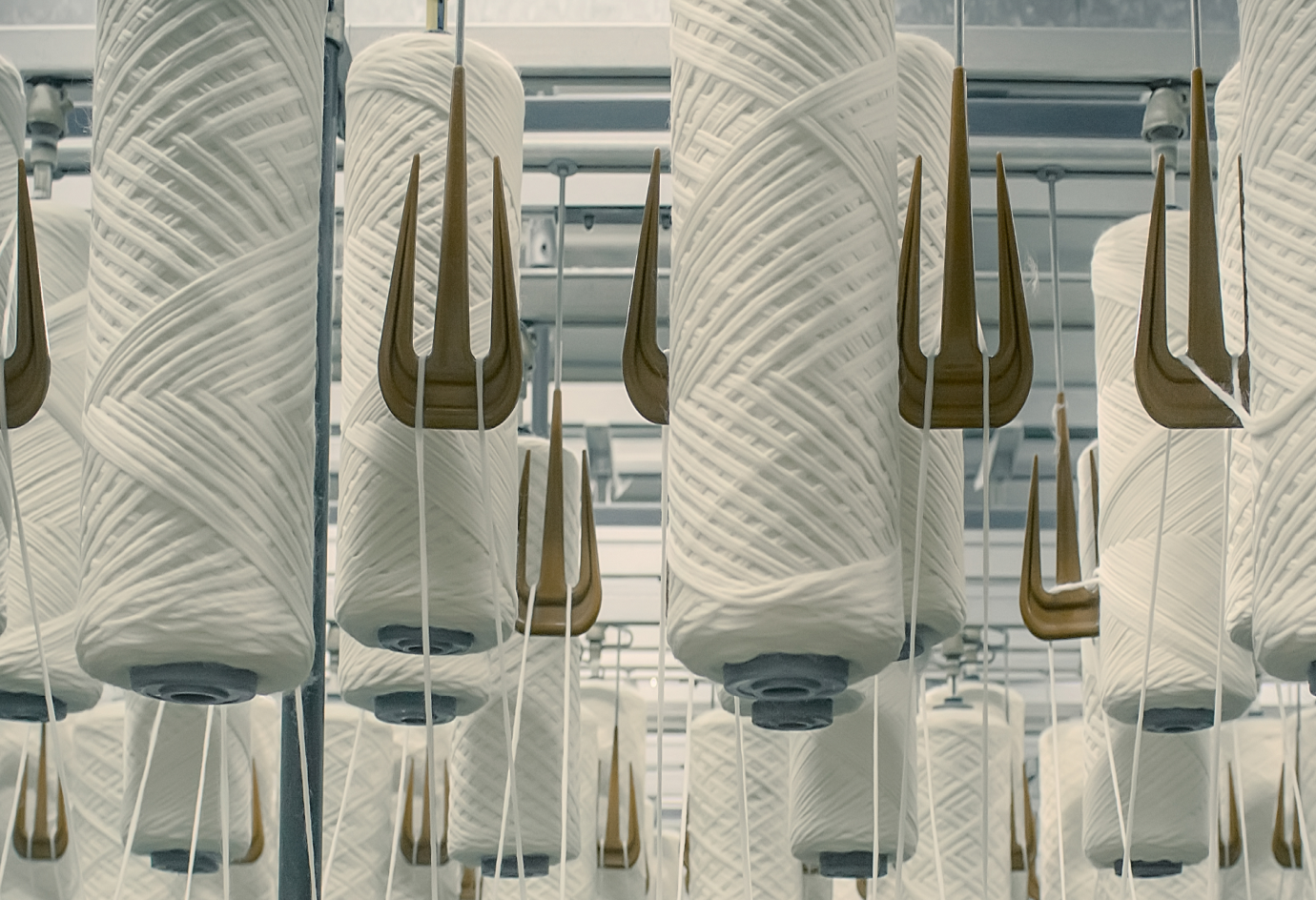
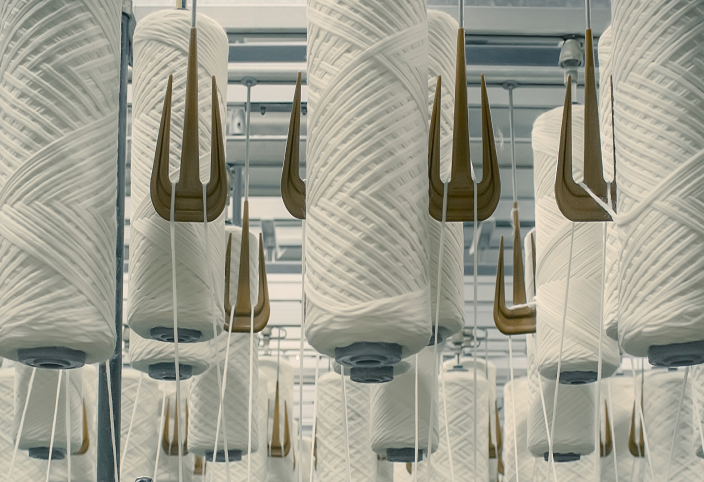
The luxuriously soft feel of Sunspel’s range of merino jumpers and lightweight dyed garments comes from the extra fine ecru yarn. Spinning the 19 micron fibres requires specialist expertise: our extra fine Merino is crafted by a business established in 1817, in the heart of the northern Italian wool industry since the Middle Ages. Like Sunspel, they insist on using ethical, non-mulesed wool and all garments conform to rigorous OEKO-TEX standards.
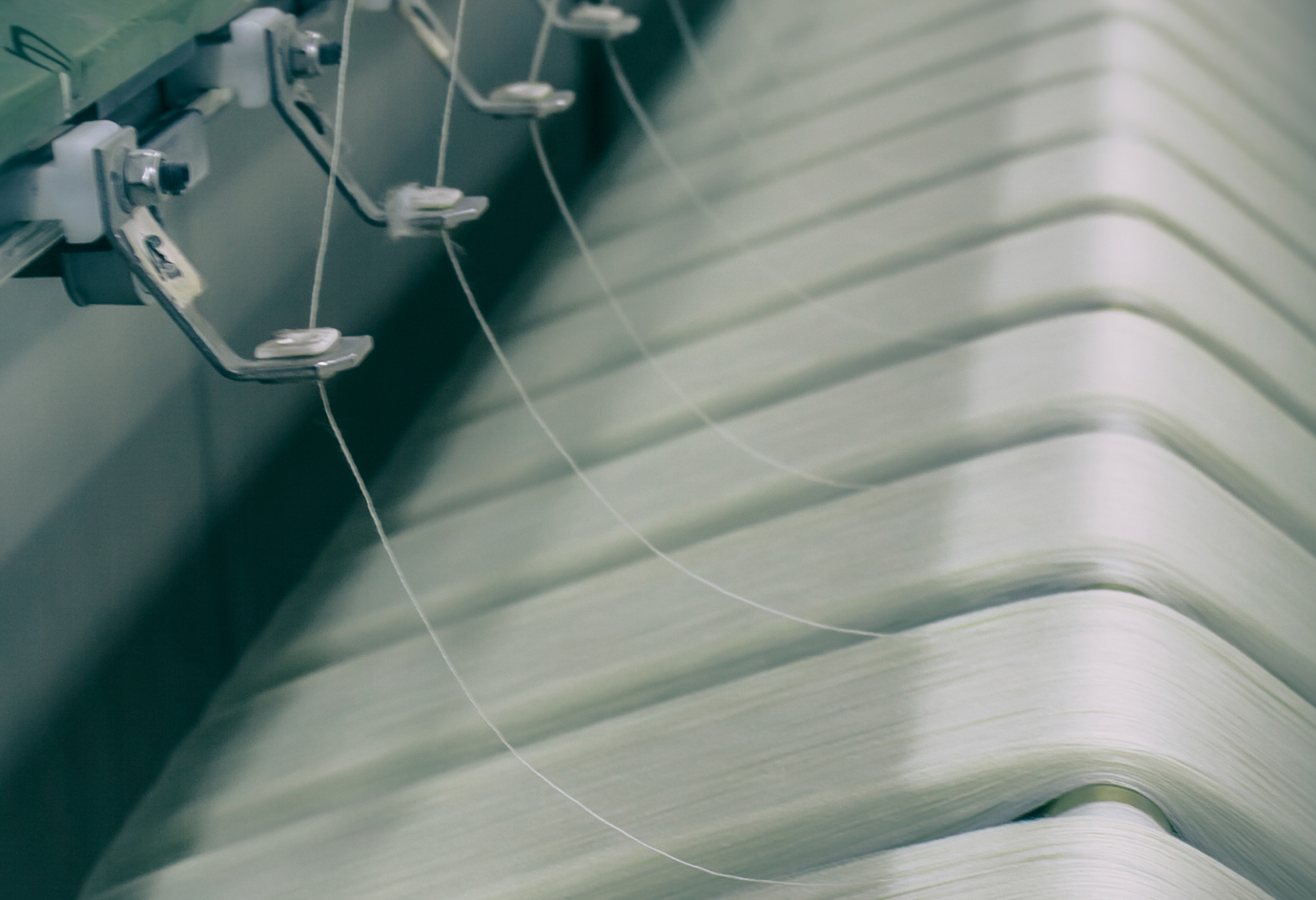
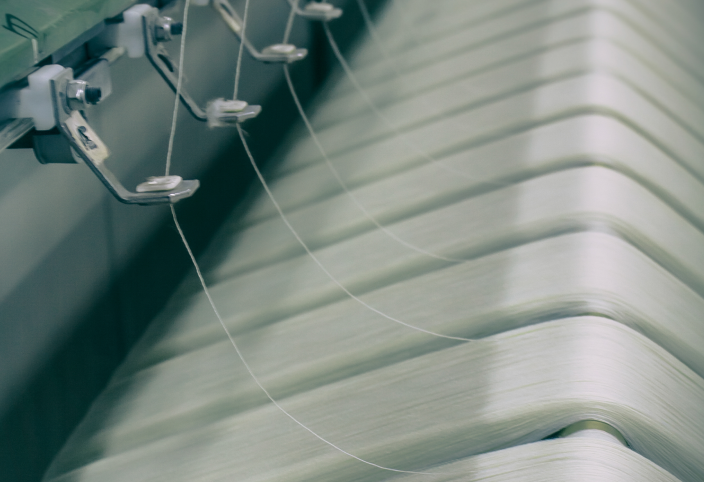
The Merino wool yarns used for Sunspel jackets and knitwear are made by a specialized yarn spinner in the Piedmont town of Biella, the area rich in textile industry tradition. The use of ethical wool and ecologically harmless substances to produce the garments is another benefit, besides the wearing comfort of the natural fibres.
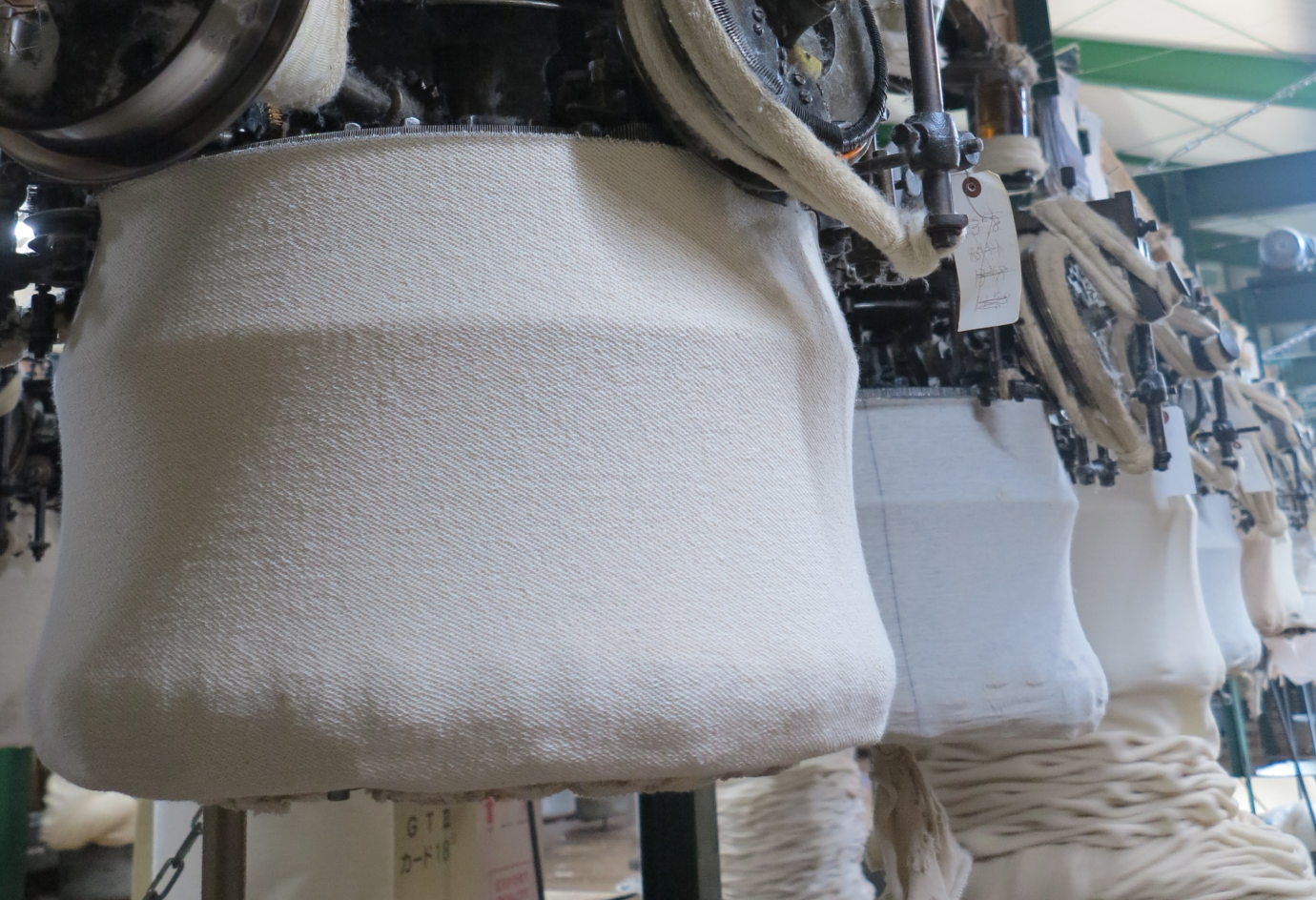

Cotton loopwheel knitting is a traditional handcraft that all but disappeared during the 20th Century. Our partner in Wakayama – the heart of the Japanese loopwheel industry – has a passion to revive the technique in Japan and pass it on to the next generation. The process uses a loopwheel machine which is hung vertically in the manner of a temple bell and knits the fabric while spinning. The technique is laborious and time-consuming, but the resulting cotton fabric is exceptionally soft and durable.
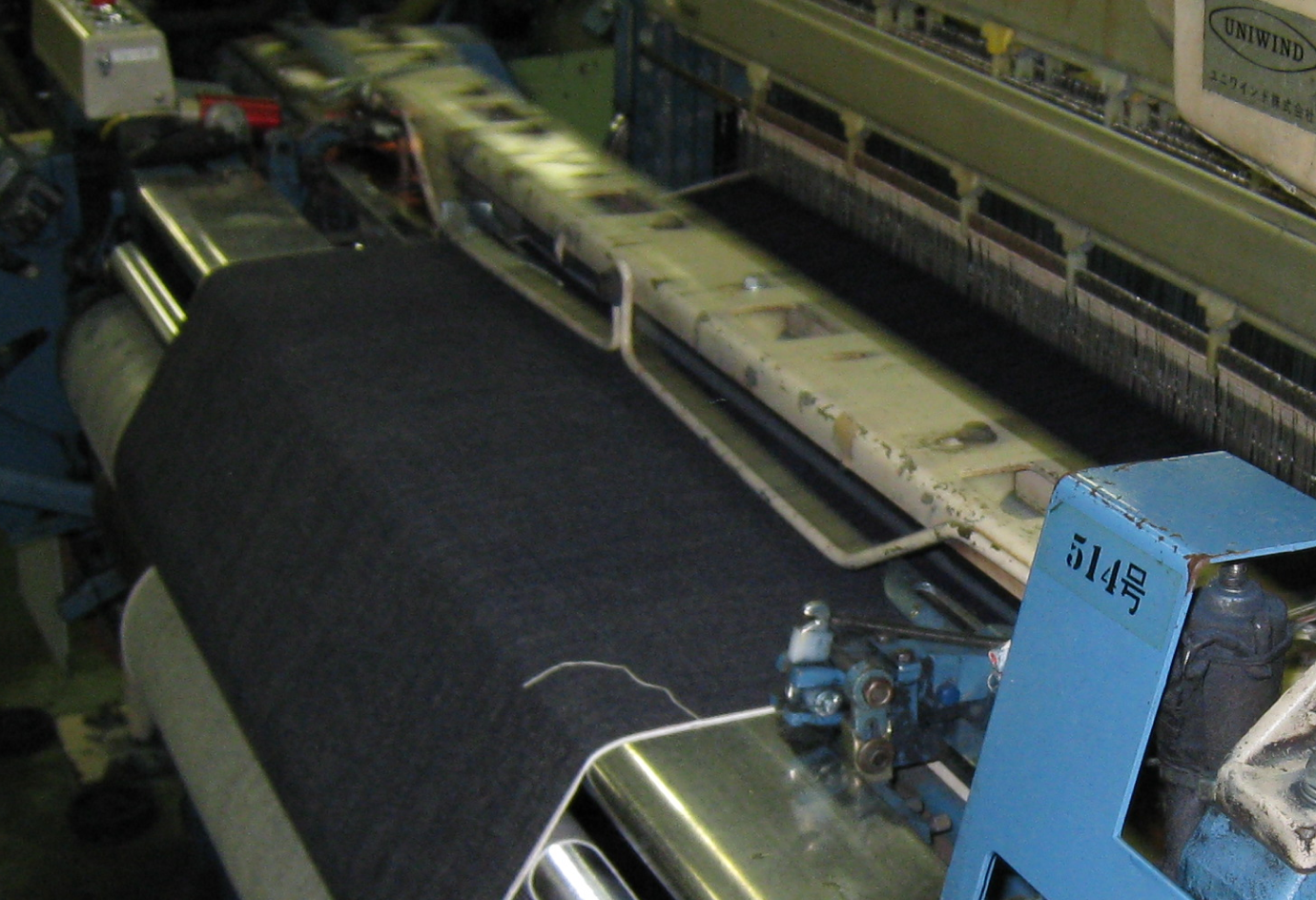

Our partners in Ibara, Okayama specialise in the total production process of rope-dyed denim, from dyeing and weaving to finishing. Ibara is a city with an abundance of naturally soft, pure water, and our manufacturers use this water to create a uniquely soft Japanese denim. Their process is extremely environmentally conscious: all water used is treated to a strict safety level, so that it can be returned to the river and used in the vegetable fields and rice paddies of Okayama.